Injection Stretch Blow Molding (ISBM) Machines: Revolutionizing Precision Container Manufacturing(A)
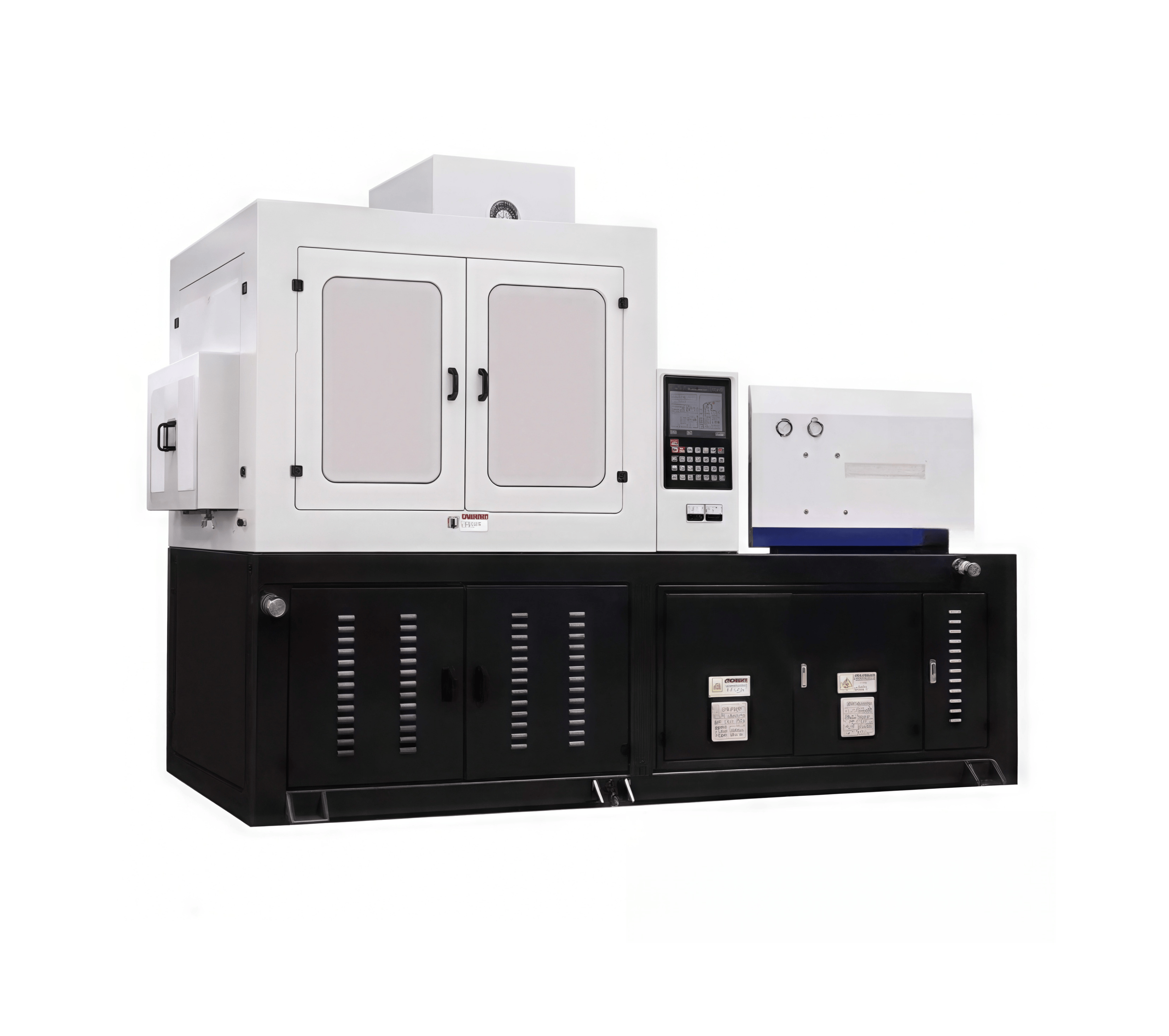
**Introduction**
Injection Stretch Blow Molding (ISBM) machines represent a pinnacle of efficiency in modern plastic container production. Combining injection molding and blow molding technologies, these advanced systems are widely used to manufacture high-precision, lightweight containers for industries ranging from beverages to pharmaceuticals. This article explores the working principles, key components, and industrial significance of ISBM machines.
**Working Principle**
The ISBM process involves three sequential stages:
1. **Preform Injection Molding**: Molten thermoplastic (typically PET) is injected into a mold to create a "preform" – a test-tube-shaped precursor with threaded neck finishes.
2. **Reheating & Stretching**: The preform is reheated to a semi-molten state, then mechanically stretched longitudinally using a stretch rod.
3. **Blow Molding**: High-pressure air (25-40 bar) is injected, expanding the preform radially against a cooled mold cavity to achieve final container dimensions.
This biaxial orientation enhances material strength, clarity, and gas barrier properties – critical for carbonated drinks and oxygen-sensitive products.
**Key Machine Components**
Modern ISBM machines integrate multiple subsystems:
- **Injection Unit**: Precision screw-and-barrel assembly for melting and injecting resin
- **Clamping System**: High-tonnage platens to withstand injection/blowing pressures
- **Temperature Control**: Multi-zone heating for consistent preform conditioning
- **Stretch Rod Mechanism**: Servo-controlled vertical stretching system
- **Blow Air System**: Oil-free compressors with precise pressure regulation
- **Handling Robots**: Automated pick-and-place systems for high-speed production