The Current State and Future Prospects of the Blow Molding Industry(A)
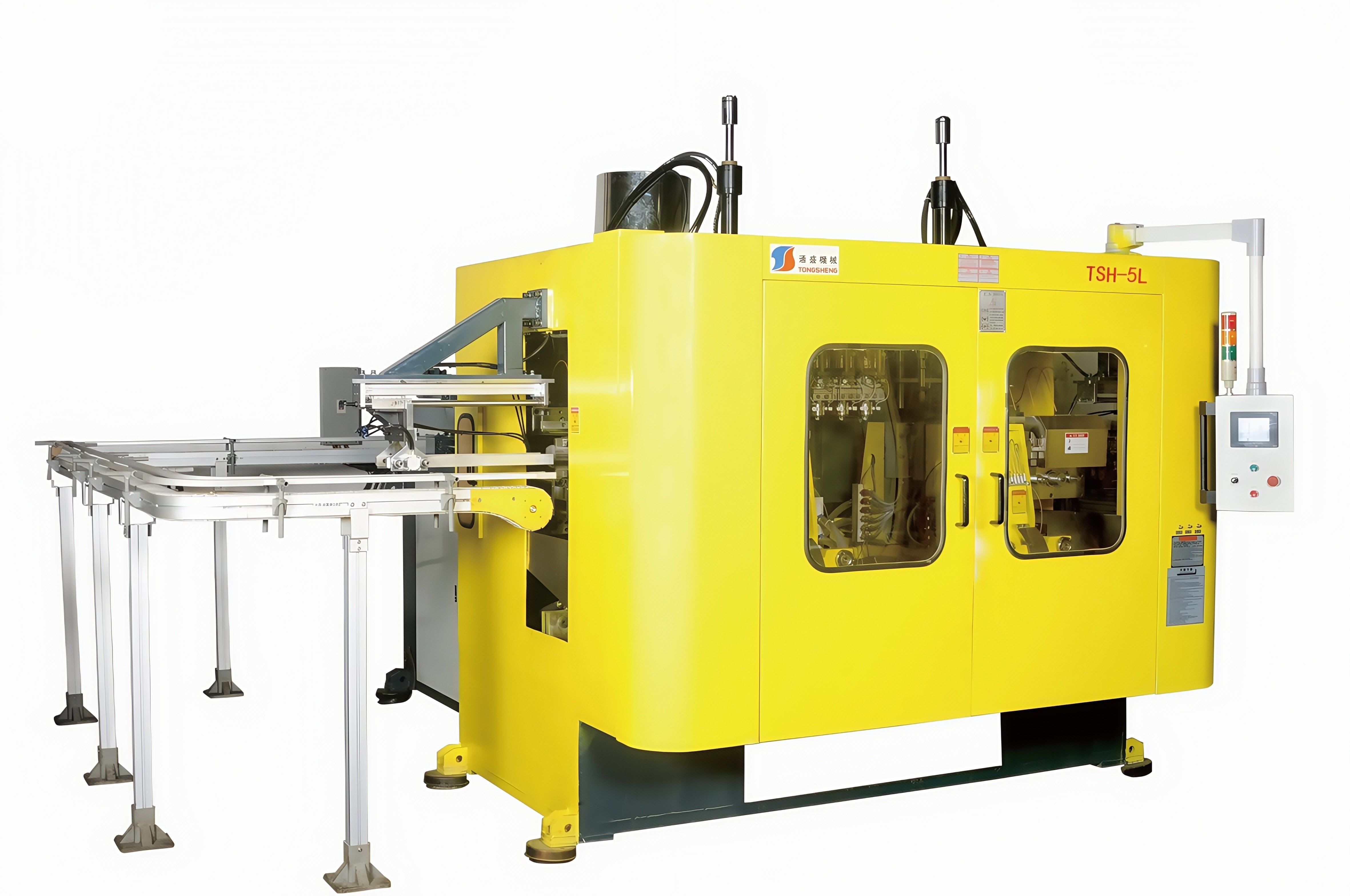
Abstract: This paper delves into the blow molding industry, examining its current state, technological advancements, market trends, environmental challenges, and future prospects. By analyzing key industry developments and market dynamics, this study aims to provide insights into the evolving landscape of blow molding and its potential for sustainable growth.
1. Introduction
Blow molding is a widely used plastic processing technique that involves inflating a molten plastic tube or preform into a mold to create hollow plastic products. This method is employed in the production of various items, including bottles, containers, and other packaging solutions. The blow molding industry has witnessed significant growth in recent years, driven by advancements in technology, increasing demand for plastic products, and the need for efficient and cost-effective manufacturing processes.
2. Current State of the Blow Molding Industry
2.1 Market Overview
The global blow molding market has shown robust growth, fueled by the escalating demand for plastic packaging, particularly in the food and beverage, pharmaceutical, and personal care industries. According to market research, the PET blow molding machine market alone is projected to maintain a steady growth trajectory, with a compound annual growth rate (CAGR) indicating continued expansion until at least 2028.
2.2 Technological Advancements
Innovation has been a cornerstone of the blow molding industry's development. Manufacturers are increasingly adopting advanced technologies such as automation and simulation software (e.g., MOLDFLOW, POLYFLOW) to optimize processes, enhance product quality, and reduce waste. These technologies enable more precise control over the blow molding process, leading to improved efficiency and sustainability.
2.3 Environmental Concerns
Despite its growth, the blow molding industry faces significant environmental challenges, particularly related to plastic pollution. The overproduction and improper disposal of plastic products have led to widespread environmental degradation. In response, industry players are focusing on developing eco-friendly materials and recycling processes to minimize their environmental footprint.
1. Introduction
Blow molding is a widely used plastic processing technique that involves inflating a molten plastic tube or preform into a mold to create hollow plastic products. This method is employed in the production of various items, including bottles, containers, and other packaging solutions. The blow molding industry has witnessed significant growth in recent years, driven by advancements in technology, increasing demand for plastic products, and the need for efficient and cost-effective manufacturing processes.
2. Current State of the Blow Molding Industry
2.1 Market Overview
The global blow molding market has shown robust growth, fueled by the escalating demand for plastic packaging, particularly in the food and beverage, pharmaceutical, and personal care industries. According to market research, the PET blow molding machine market alone is projected to maintain a steady growth trajectory, with a compound annual growth rate (CAGR) indicating continued expansion until at least 2028.
2.2 Technological Advancements
Innovation has been a cornerstone of the blow molding industry's development. Manufacturers are increasingly adopting advanced technologies such as automation and simulation software (e.g., MOLDFLOW, POLYFLOW) to optimize processes, enhance product quality, and reduce waste. These technologies enable more precise control over the blow molding process, leading to improved efficiency and sustainability.
2.3 Environmental Concerns
Despite its growth, the blow molding industry faces significant environmental challenges, particularly related to plastic pollution. The overproduction and improper disposal of plastic products have led to widespread environmental degradation. In response, industry players are focusing on developing eco-friendly materials and recycling processes to minimize their environmental footprint.